VT – Visual Inspection
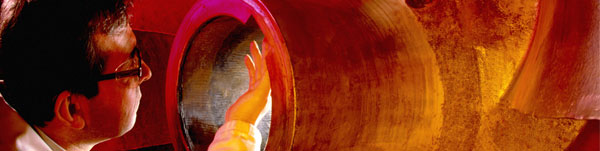
Sight check
is an optical inspection of a product or part for defects and blemishes as a conventional step in the production process at the end or after completion of the manufacturing of a product for quality control reasons. Sight checks are also performed on operating parts. Visual inspection as a non-destructive testing method is standardised according to DIN standard DIN EN 13018 (General principles of visual inspection).
This standard is distinguishing between:
- Direct visual inspection without any additional tools (inspection of the object with the naked eye).
- Direct visual inspection including additional tools (optical devices e.g. magnifying glasses, endoscopes, mirrors).
- Indirect visual inspection (with cameras, videoscopes etc.).
The distinction between direct and indirect visual inspections is defined in the standard as follows:
- Direct visual inspection = Visual inspection without interruption of the optical path between inspected object and the eye of the observer.
- Indirect visual inspection = Visual inspection with interruption of the optical path between inspected object and the eye of the observer, this means transformations of the light beam to a different form of energy, thus in electrical information (camera).
Typical defects that should be detected by a visual inspection
are mechanical damage (scratches, cracks), dirt settlings, assembly errors, feathering, end-crater-cracks and undercuts. Alongside colour changes (annealing colours at e.g. austenitic steels), surface roughness etc. can be discovered effectively.
|