UT – Ultrasonic testing
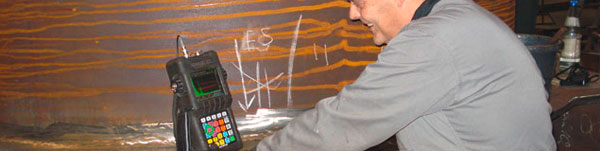
Ultrasonic testing
The ultrasonic testing is an acoustic method for detecting material defects and is a non-destructive testing method. Thus it is possible to test components when installed e.g. components of an aircraft.
Like all the other testing methods the ultrasonic testing is standardised and is implemented according to the guidelines. For this process a coupling aid (e.g. glue, gel, water or oil) is applied on the surface of the tested object. By means of a probe, which emits and receives ultrasonic waves between 0.2 MHz and 50 MHz the tested object is scanned. This can be done manually, mechanised or automatically (on the production lines). At the latter, the tested object is dipped in a suitable liquid (dipping technique) or moistened for better transmission of the sound signal.
Changes of the acoustic characteristics at edge surfaces (e.g. a cavity, an inclusion, a fissure or another separation of the material) inside the tested object reflect the ultrasonic impulse and send it back to the probe, which works as an emitter and as a receptor. The passed time between sending and receiving the signal makes it possible to calculate the distance (pulse-echo method). With the calculated time a signal pattern can be provided and visualised on a screen. The picture indicates the position, while the size of the discontinuity can be determined by comparing it with a second reflector (flat bottom hole, reflector, flute, cross-hole).
Ultrasonic wall thickness measuring systems indicate the wall thickness after calibration as a decimal number.
Scope
The ultrasonic testing method is an appropriate tool for sound-conducting materials (most metals belong to this group) for detecting internal and external flaws e.g. at welds, forged pieces, cast iron, wrought material and pipes. Railway tracks are tested routinely with special testing trains. The detection of external (surface-) flaws is especially important for parts, where the inside of the material cannot be tested.
Procedure
There are two general procedures which can be utilized:
1) Reflexive acoustic method (Impulse-echo method)
The tiniest discontinuity that can be detected is bigger than half of the wave-length of sound, which depends on the sound velocity of the tested material and the frequency of the probe. At a frequency of 4 MHz the discontinuity in steel amounts to 0.7mm. The height of the frequency cannot be increased limitlessly, since the particle size of the structure leads to diffusion and absorption and therefore the depth of penetration is reduced. The rougher the crystallisation in e.g. cast steel is, the longer the waves of the chosen sonic frequency. For cast iron or austenite, the testing methods are usually very limited. The longest distances that can be scanned with the impulse-echo method are up to 5 meters, which equals a sound path of 10 meters. The smallest resolution would be the wall thickness measurement of a razor blade with a 50 MHz probe.
2) Through-transmission method
This process includes two probes, which are attached to one ultrasonic device. One probe sends the impulse while the other receives the impulse on the exact opposite side of the tested part. This method is very specific and is usually needed for the detection of flaws. The squirter-technique is an example for the combination of the dipping technique and through-transmission method. In this case the two probes are not attached to the tested object, but are attached aside each other in a distance of several centimetres and are connected through water. This technique is used e.g. at Airbus for large-area testing of CFK/GFK tail unit components.
Special testing method
There are approximately forty different special testing methods and new methods are added every year. A special testing method is understood as the usage of acoustic effects in materials aside from the “classic” detection methods. Important methods are e.g. Phased Array, TOFD etc. Sometimes they only differ in the way of signal processin.
Picture gallery
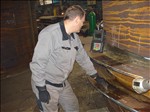 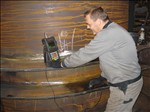 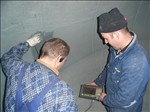
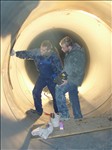
|