PT – Dye penetrant test
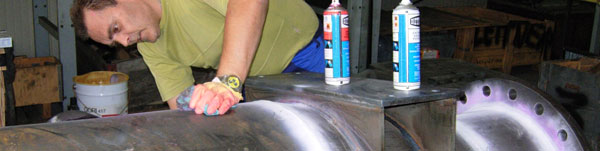
The penetrant test (according to ÖN EN ISO 3452-1: penetrant test, general principles) is a non-destructive testing method which uses capillary forces of fine surface cracks and porosities to make these visible. There is a distinction between dye penetrant test and fluorescent penetrant test.
- Cleaning
- Application and penetration of colour
- Shallow cleaning
- Application of developer
Dye penetrant test
For this procedure the surface of the component to be tested is stripped of oil and fat remainders and afterwards the penetrant is applied. This can be achieved by using a brush, dipping in a bath or, in well ventilated areas, by spray coating (all of these mentioned methods are also called forced wetting). The creeping ability of the penetrant is very high, uses capillarity of the finest material separations and possesses a high colour contrast for the developer.
With the dye colour penetrant test it is possible to find cracks on the surface of materials easily (up to one thousands of a millimetre width). However, pseudo exposures can occur on rough or ridged surfaces. These indications are defects. Furthermore this testing method does not indicate the depth of the defects concerning the intensity of indication: a delicate pink coloured defect does not necessarily indicate a less deep crack than a dark red indication.
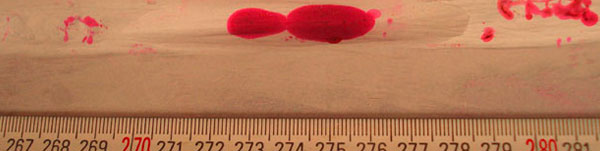
Fluorescent penetrant test
When the ambient brightness is too low, fluorescent penetrants are used, which can be visualised with ultraviolet radiation. This testing method is considerably more sensitive than the dye penetrant test, since the fluorescent particles produce a luminance contrast. The human eye reacts far more sensitive to luminance contrasts compared to colour contrasts.
The penetrant test is applicable to all materials which allow a definite indication of surface defects (not poriferous), mainly used on metals, plastics (with limitations: e.g. Teflon), glazed ceramics and the like. For machine parts made of steel a solvent-based developer is applied due to the high corrosion susceptibility. For ferromagnetic (non-austenitic steels) the magnetic particle testing is performed.
Picture gallery
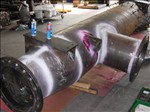 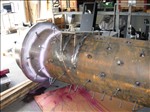 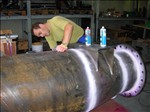
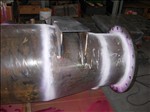
|